How can manufacturers reduce downtime & boost productivity with real-time data monitoring
It is 2023, and we are well and truly in the technology and data-driven age of Industry 4.0. However, many European companies are still in the early stages of transitioning into smart manufacturing. According to a survey of 1,452 corporate decision-makers in top European firms, only 23% have started the digital transformation of their production. Companies that have fully upgraded their operations to the standards of Industry 4.0 are experiencing benefits such as increased efficiency, improved quality, and reduced costs.
One of the key contributors to the advancements in the manufacturing industry is real-time data monitoring. This transformative technology is becoming increasingly crucial because it can revolutionize manufacturing operations, fostering more informed decision-making, and optimizing production processes.
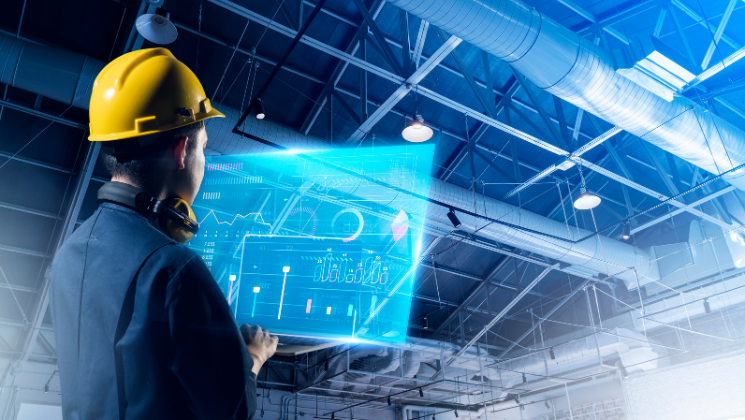
Real-time data monitoring: the manufacturing game-changer
Real-time data monitoring (RTDM) is the continuous collection and analysis of data at zero to low latency. It involves systematic monitoring of data streams as soon as it is generated to keep users updated about the current state of their systems or operations. Consequently, organizations can detect and respond to significant changes at the point of occurrence. The advancement in technology has made specialized software and tools available, and this has allowed organizations across different industries to visualize and analyze data in real time and optimize numerous aspects of their operations seamlessly.
Real-time data monitoring is definitely applicable to the manufacturing industry, where every company strives for production efficiency and supply chain maximization. Implementing this technology enables real-time tracking and analysis of various key performance indicators (KPIs), such as production rates and machine health status. The ability to capture fluctuations and changes in data streams as fast as milliseconds after they occur and immediately act on these new insights opens a world of endless possibilities for manufacturers.
According to KX’s Microsecond Mindset study, 68% of UK manufacturers saw significant to moderate cost reductions resulting from anomalies after implementing real-time data systems. This same study showed that manufacturing companies in Germany were able to increase revenue by 36.8% with real-time data. Statistics such as these prove that monitoring and analyzing data in real-time boosts efficiency in critical manufacturing processes, ensuring that production operations continue at optimal levels round-the-clock at the lowest possible costs. Investing in this technology is great news for customers, too, because it means manufacturers can meet and exceed their expectations by releasing high-quality products all year round.
Applications of real-time data monitoring in the manufacturing industry
Real-time monitoring of manufacturing assets provides varying benefits depending on the manner and extent to which the decision-makers choose to apply this technology. Here are the key ways in which companies can apply real-time data systems in manufacturing to truly transform their production processes:
Minimizing downtime with proactive and predictive maintenance
Real-time data monitoring enhances visibility, and forward-thinking organizations can take advantage of this to implement proactive intervention measures that significantly reduce machine downtime. Considering the powerful technology available today, the days of reactive maintenance when companies waited for equipment failures and breakdowns before taking action should be long behind manufacturers. Now, there are sensors that collect information on temperature, vibration, pressure, oil analysis, and machine health indicators in real time. This data provides up-to-date information about the equipment’s health and performance.
With the updated information, manufacturers can perform condition-based monitoring. Maintenance activities are scheduled when real-time data streams indicate impending critical failure. Also, businesses can go a step further by using the Industrial Internet of Things (IIoT) to connect sensors to sophisticated, AI-powered software that can accurately predict equipment breakdowns. Either way, manufacturers can be proactive about their intervention measures through early failure detection and prompt scheduling of repairs. According to McKinsey, predictive maintenance reduced machine downtime by 30-50% while prolonging machine lifespan by as much as 40%, making it a strategy worth investing in.
Achieving peak levels of quality control and product traceability
Manufacturers strive to produce high-quality products, and real-time data monitoring enhances their capacity to achieve that through quality control and product traceability. Continuous data collection and analysis allow manufacturers to detect even the slightest deviations from the predefined quality standards set on the production floor and take corrective measures immediately. For example, a sensor might detect a deviation in product size during manufacturing, prompting the team to correct the anomaly. Hence, product quality is always maintained at the intended levels.
Similarly, real-time data monitoring ensures that products are traceable through every step of the production process, from raw material sourcing down to distribution. With this tracking power, manufacturers can easily identify the root cause of problematic products and implement corrective actions swiftly to prevent reoccurrence. Product traceability also means it becomes easy to recall faulty products after distribution and enforce regulatory compliance throughout the organization.
Empowering stakeholders for strategic and informed decision-making
With real-time data monitoring, decision-makers can access insights within seconds after they are generated for faster decision times. Data arising from the production floor can reveal the difference between targeted production rates, cycle times, downtimes, and quality metrics and what is being obtained at the manufacturing plant. This enables the key stakeholders to make informed, strategic, and data-driven decisions and optimize production processes for maximum efficiency.
For example, real-time visibility into the production processes can inform decisions on resource allocation. By monitoring production from the stage of raw material acquisition till finished products reach the final consumers, manufacturers can identify points where more human or material resources are required. Real-time insights also reveal opportunities continuously optimize workflows and operations, eliminating gaps and lapses hindering operational excellence in manufacturing.
The evidence that real-time data monitoring works: two manufacturing case studies to consider
Implementing real-time data monitoring is becoming a more popular practice in the manufacturing industry, and there are success stories to show for it. An example is that of a UK-based global automotive company that struggled with a lack of actionable production data. Consequently, their manufacturing processes were plagued with significant downtime and losses. A drastic improvement in that dire situation was made when the automaker opted into a centralized platform for collecting and monitoring real-time data throughout the organization. This provided their team members with live data and valuable insights for smarter decisions, resulting in better product quality and higher performance. The automaker also experienced better equipment availability, with an 18% improvement in Mean Time to Repair (MTTR) and Mean Time Between Failure (MTBF).
Rolls-Royce has also implemented a similar solution for its jet engines. As one of the largest makers of aircraft engines in the world, the British manufacturing company faces significant pressure to keep planes and jets running on their engines in the air longer. To meet up with this expectation, Rolls-Royce developed the Intelligent Engine platform through which it captures real-time data from each engine as the aircraft flies. Data analysis follows, and the company has been able to make data-driven decisions promoting productivity and predictive maintenance. Their platform has helped extend the time between maintenance for some engines by as much as 50% while improving the efficiency of all engines.
Transforming your manufacturing operations with ACTUM Digital
Real-time data monitoring is a critical practice shaping the industry's future. As demonstrated in the case studies above, this technology has the potential to maximize productivity, minimize downtime, optimize processes, and deliver high-quality products that generate more revenue and delight customers. Hence, your company’s next step should be unlocking the potential of this transformative technology.
Implementing real-time data monitoring solutions requires a complex integration of sensors, analytical tools, and existing systems. ACTUM Digital can help you navigate this complex process through our tested and trusted system integration services. Work with our team of certified experts to develop a strategic and long-term plan for integrating this leading technology into your existing data systems to take your manufacturing operations to new levels of excellence.
You may also like...
[19/05/2023] How Big Data Analytics Impacts Manufacturing & Supply Chain
Unleash endless possibilities in manufacturing supply chain operations with big data analytics. Discover implementation steps for maximum benefits.
Read the Insight[04/05/2023] Optimizing Production Efficiency with Predictive Maintenance
In the rapidly evolving world of manufacturing, efficiency remains a constant watchword. Businesses are continuously searching for new methods and strategies to boost efficiency...
Read the Insight